Hardwood lump charcoal is a favorite among BBQ enthusiasts for its pure, smoky flavor and high heat. It’s essential to distinguish it from coconut charcoal briquettes, which often contain additives or binders. Hardwood lump charcoal is made by burning wood until it becomes carbonized, resulting in irregular chunks that ignite quickly and provide an authentic, natural taste to your grilled dishes. Because of its versatility and clean burn, it is the go-to pick for barbecue enthusiasts who want to capture that signature smoky flavor. Remember that real hardwood lump charcoal, not charcoal briquettes, provides the best grilling experience possible.
Here at Grand Royal Coco, we produce hardwood lump charcoal at its finest while keeping environmental sustainability in mind. We only use wood waste from the lumber industries as our raw materials so that no new trees are cut down for production purposes. We source the best types of hardwoods that produce a high heat level with a long burning time such as mahogany, acacia, tamarind, fruitwoods, and teak wood. They have high calorific values of up to 4,000 calories with a long burning time of up to 4 hours, making them perfect for heating and grilling applications.
We strictly adhere to our production standards from the raw material selection to the packaging process to yield the best quality hardwood lump charcoal with a high fixed carbon of up to 80%, minimum ash below 2%, and low moisture of less than 5%. These specifications translate to a long burning time, and a high heat level and do not produce any sparks or smoke when burned. In addition, our hardwood lump charcoal releases a naturally pleasant wood aroma that generates a calming effect, enhances the flavor and elevates your barbeque experience.
Crafting Excellence: The Secrets Behind Our World-Class Hardwood Lump Charcoal
So let’s get down to business. How do we make one of the world’s best hardwood lump charcoal in the market? What we are about to share with you are truly tried-and-true methods that have been perfected over many years, making sure that every piece of charcoal we make is of the highest quality. Here are the long-kept-secret steps:
1. Choosing Raw Materials for the Hardwood Lump Charcoal
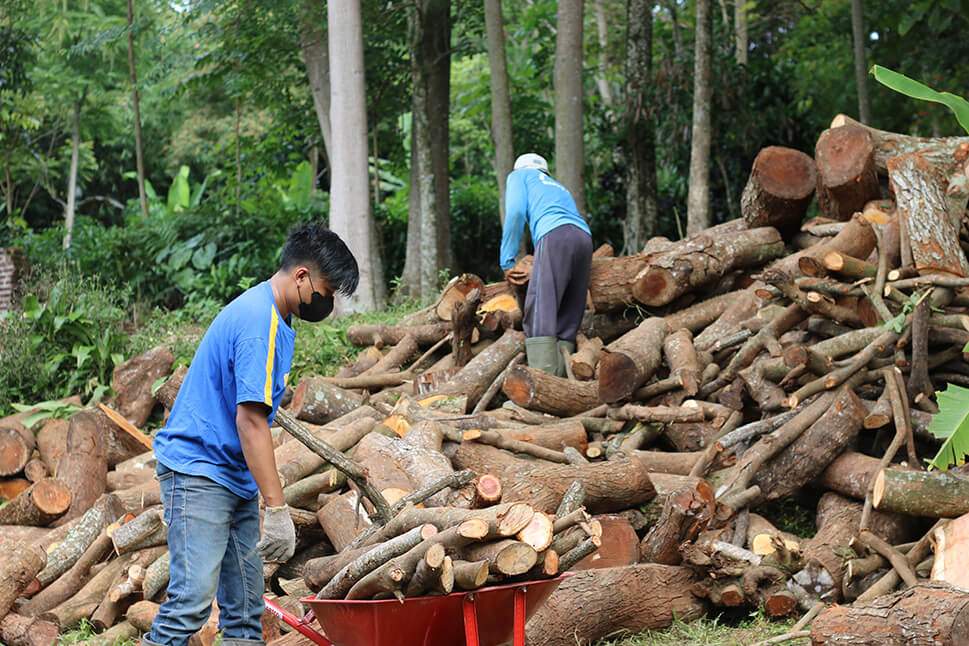
We use mahogany wood waste, particularly the branches and twigs as our raw material in our charcoal production because it produces a high heat level with a long burning time. In addition, mahogany woods are relatively more readily available than any other types of hardwood such as teak. Mahogany trees are also known to have a shorter harvest period compared to teak trees, contributing to a more sustainable and efficient production process. Acacia wood, known for its durability and excellent burning properties, has also earned its top place among our preferred hardwoods.
It is worth noting that not all types of hardwood trees are suitable for making hardwood lump charcoal. Take rubber trees, for instance. Although classified as hardwoods, it contain a lot of sap with high moisture content that lowers the heat output, reduces burning time and causes sparks when burned. Therefore, careful selection of hardwood material is crucial in crafting the highest-quality lump charcoal.
2. Placing Hardwood Lumps into the Charcoal Kilns
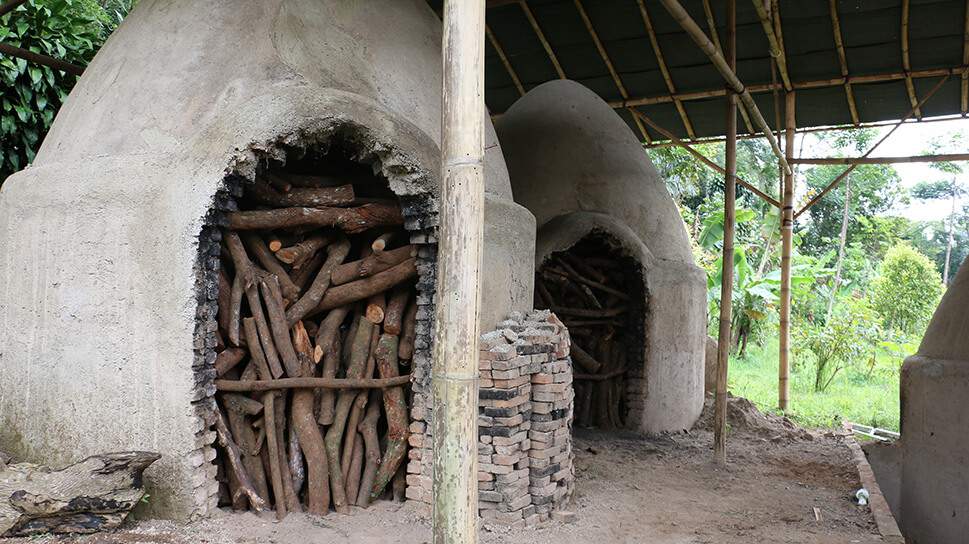
3. Sealing the Charcoal Kilns
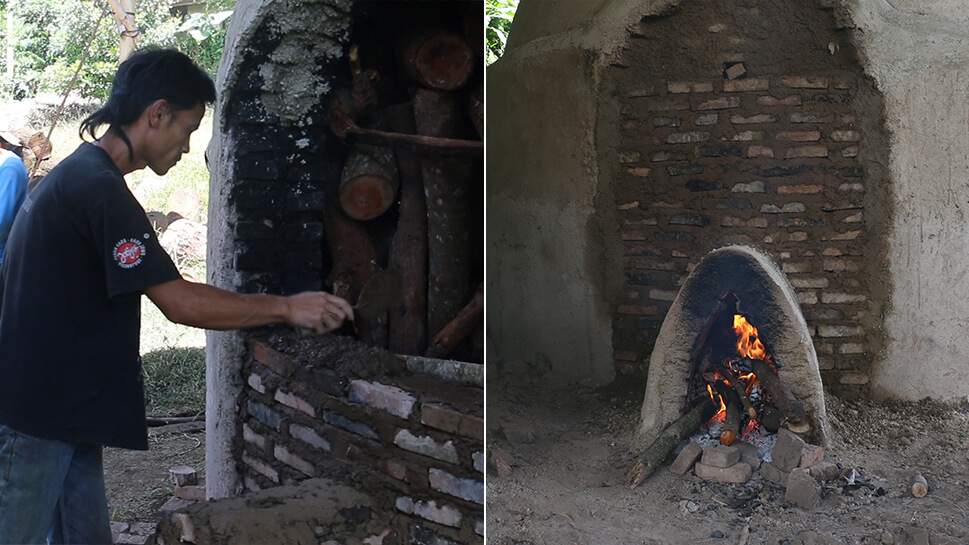
Once the hardwood waste is properly arranged, we start laying bricks to completely seal the kilns with the aid of sand and cement while leaving a hole at the front for burning the wood fuel and small holes at the sides to vent out any residue resulting from the burning process.
It is important to properly seal the kiln to block any wind and minimize the amount of oxygen present in the carbonization process to ensure the resulting charcoal contains a high percentage of fixed carbon and high calorific values.
4. Burning the Hardwood Lumps
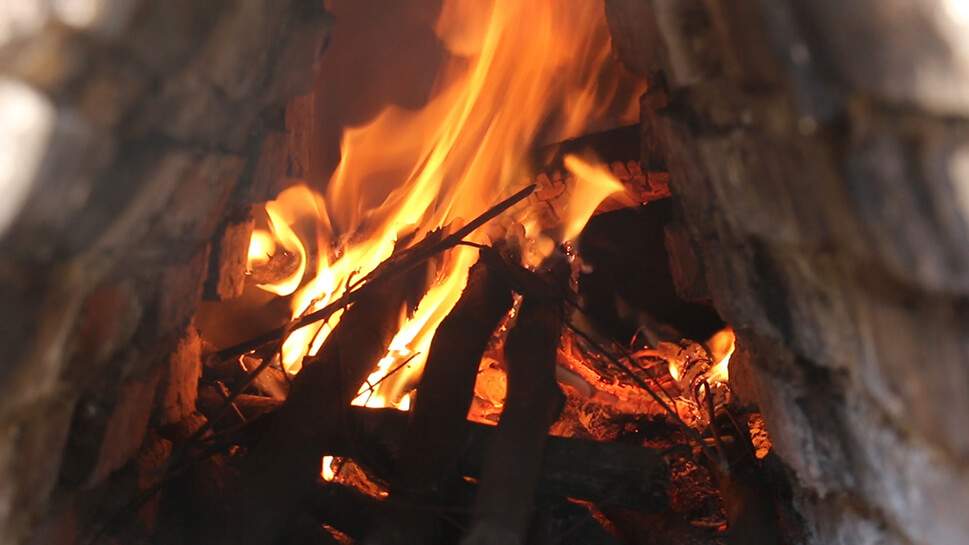
Once sealed, the carbonization occurs indirectly through the hot steam produced by the combustion of the wood fuel at 400°C for 5 days in a low oxygen environment. The dome shape of the kiln helps keep the temperature constant throughout the process for optimal carbonization.
As the hot steam gradually carbonizes the hardwood lumps, methane, hydrogen and tar residues are released and vent out through the holes at the sides of the kilns.
5. Cooling the Hardwood Lump Charcoal with the “Dry Method”
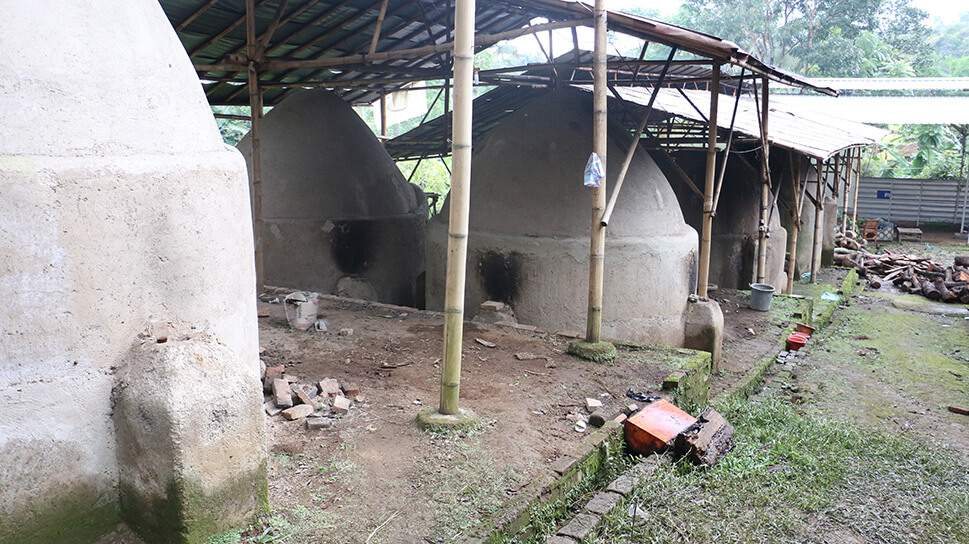
6. Removing the Hardwood Lump Charcoal from the Kiln
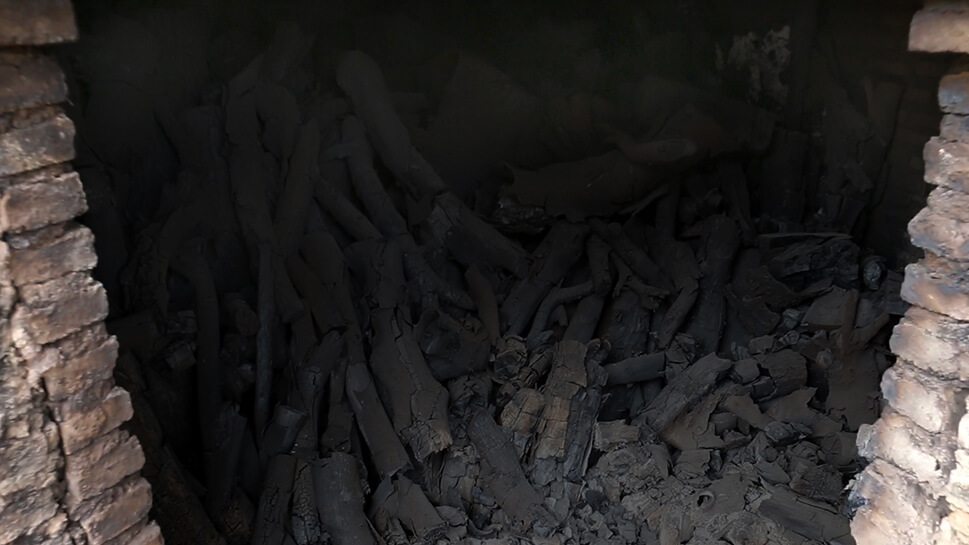
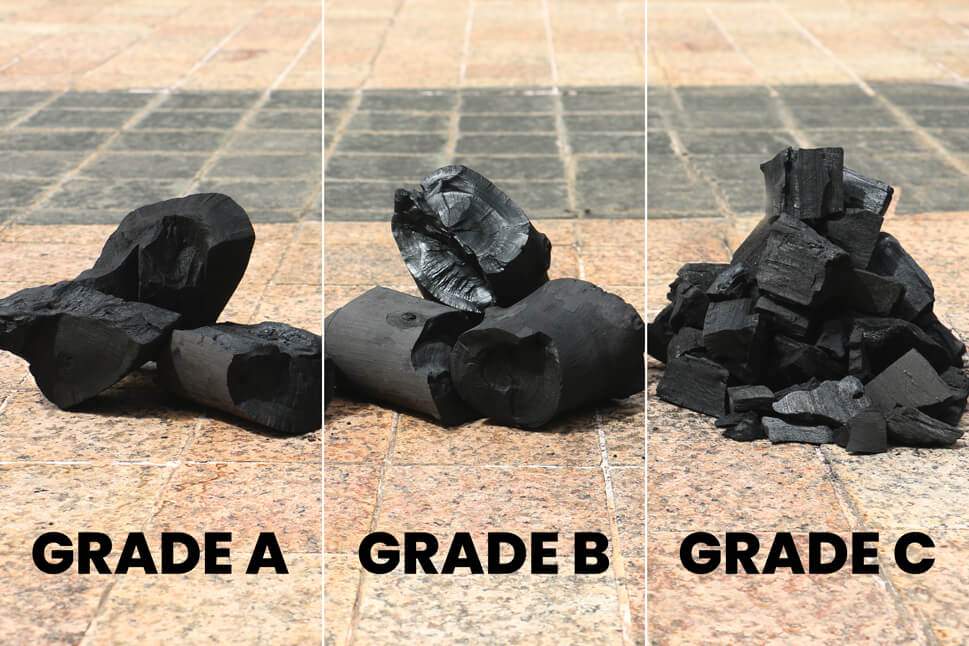
7. Packaging Process
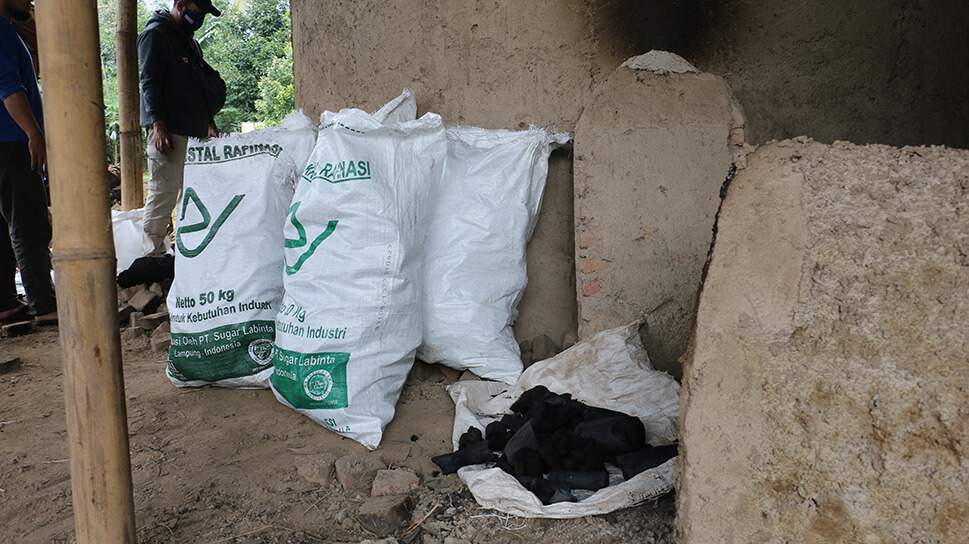
At Grand Royal Coco, we accept custom packaging requests tailored to your market needs. We offer a wide range of packaging materials and custom labels that give added value to your business. Here are some amazing packaging inspirations from the top-reviewed hardwood lump charcoal for BBQ and grilling for your consideration when designing your custom packaging.
If you are looking to create the perfect charcoal product for your market at scale and take your charcoal business to the next level, get in touch with us now for a free consultation and find out how we can best help you. We’ll work closely with you to come up with a plan that best fits your goals and strategy. From helping you choose the best hardwoods for your lump charcoal to coming up with custom packing solutions and reliable shipping services, we are here to ensure your success. Let us help you turn your charcoal business into a thriving market-leading enterprise starting today.